About Us
Our Facility
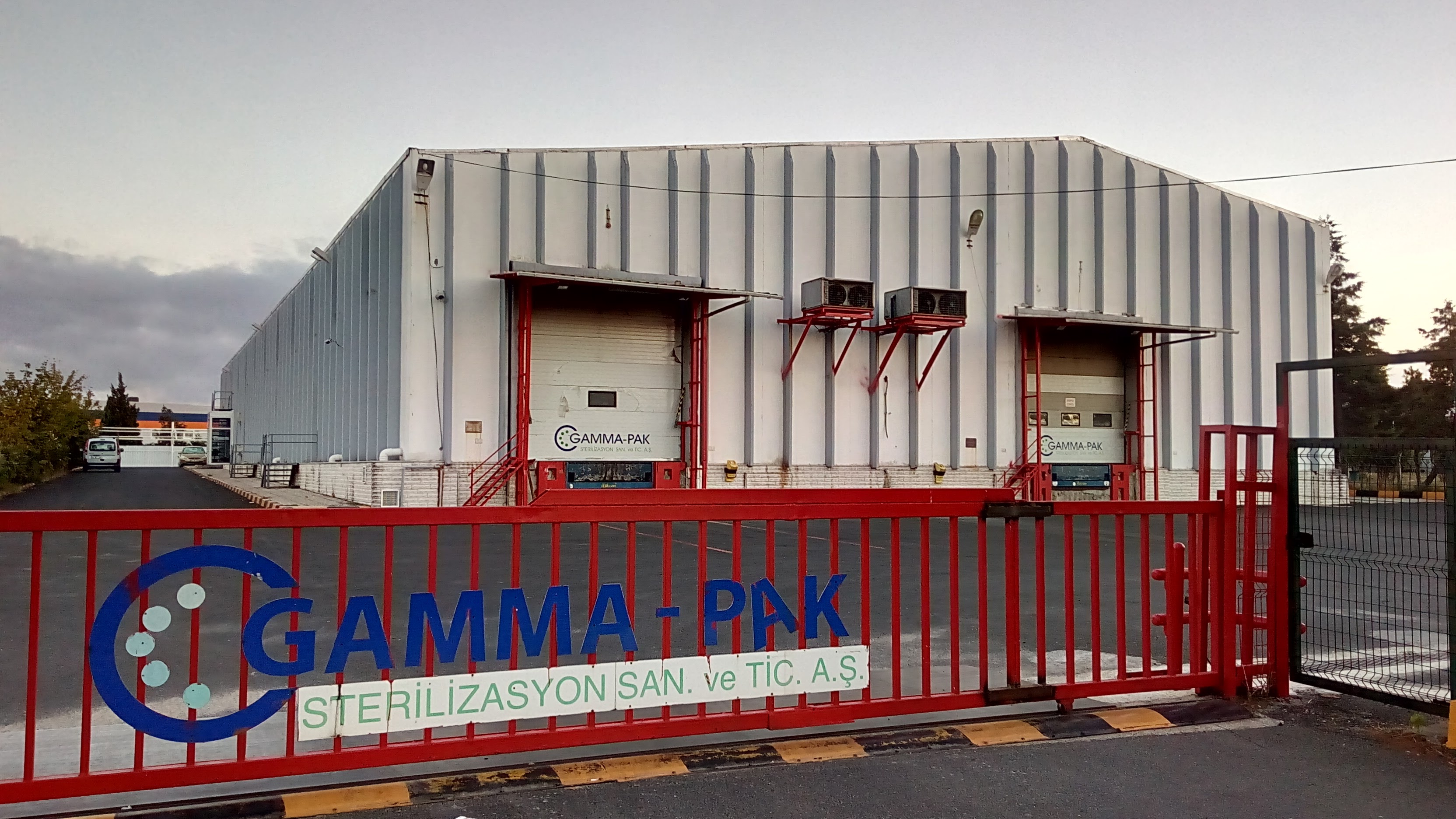
Gamma Pak was founded in Çerkezköy, Istanbul, Turkey in 1994 to meet the demand for products sterilized with gamma rays, to prevent food losses, to increase the shelf lives of the products and to provide the demanded changes in polymer materials.
Gamma Pak is able to irradiate seven food groups permitted by "Food Irradiation Code" and it is the only and the biggest irradiation company in Turkey approved by the European Commission on Oct., 7th, 2004 in Turkey.
Our facility is in The Çerkezköy Organized Industrial Area in Tekirdağ. It was built on an area of 12400 m2 and has a covered area of 2420 m2, 1500 of which is storage area.
QUALITY
Gamma Pak is working hard with its qualified experts to meet and go beyond the demands of its customers and is very keen on being honest and ethic.
For this objective, Gamma Pak received;
TS EN ISO 11137-1 and
TS EN ISO 22000
quality management system certificates and implementing them carefully.
All the quality and management systems implemented in our company are monitored and inspected periodically and thus efforts are exerted for the continuous enhancement of the system by fulfilling the requirements of current legal laws and regulations and international standards.
IRRADIATION FACILITY
Gamma Irradiation Device is JS 9600 model 4th category and automatic tote box carrier type. The Irradiation Device was registered by the International Atomic Energy Agency with serial number IR-185. Radiation Device uses double encapsuled Co-60 radioactive pencils as source. The total capacity of the source panel is 101 PBq (3,000,000 Ci).
Irradiation Plant consists of Process Control (Control Room), Product Transportation System, Source and Source Rack, Irradiation Cell (Biological Shield), Source Storage Pool and Product Storage Area,
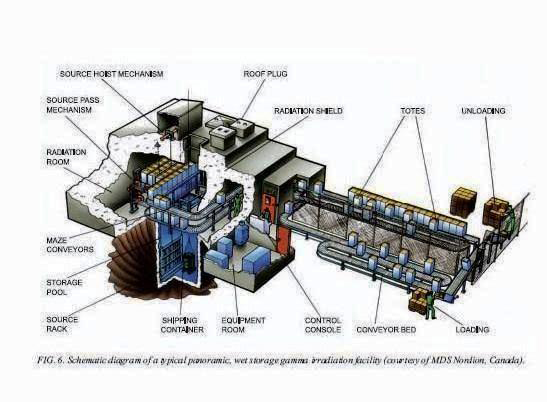
1. Process Control: In the Gamma Irradiation Facility, the irradiation process is realized by means of a powerful and reliable computer system (Programmable Logic Control), which is acknowledged in all over the world. Each stage of irradiation process is controlled in a very sensitive manner and if an abnormal case is occurred, Irradiator turns off automatically and gives audio and visual alarms. Furthermore each stage is recorded automatically.
2. Product Transportation System (Conveyor and Source transition system): The products to be processed are placed inside the aluminum tote boxes on the conveyor in their own packages and are sent to the irradiation room by means of the conveyor. The boxes full of products are moved around the source by means pneumatic pistons and exposed to gamma irradiation. After the irradiation process the tote boxes full of products are taken out automatically by conveyor and stored at the irradiated product area. The dimensions of the tote boxes made of aluminum are 58 x 64 x 124 cm and each of them can carry loads up to 125 kg.
3. Source and Source Rack: Source rack consists of a stainless steel frame with dimensions of 250x300 cm and 20 rectangular intermediate modules. 40-source pencils that are 45 cm long and with a diameter of 0.81 cm can be placed on each module. Metallic formed Co-60 slugs used as gamma source are placed in these source pencils. Source pencils are double encapsulated in stainless steel tubes and both ends are welled in a leakage proof manner. The manufacturer company of the source pencils shall protect their leakage proof characteristics for 20 years. Unstable Co-60 isotope is obtained from the stable Co-59 atom by adding a neutron into its nucleus via neutron bombardment in the nuclear reactors. Co-60 isotope emits one beta and two gamma rays with energy levels of 1.17 MeV and 1.33 MeV and transformed to stable Ni-60 atom.
Since beta particles cannot pass through the stainless steel, irradiation process is realized only by the gamma rays. The irradiated products never become radioactive whatever the irradiation period is. The energy level of the gamma rays emitted by Co-60 isotopes is not enough to make any material radioactive. Therefore in theory no treaded product by gamma irradiation process shall be radioactive.
4. Irradiation Cell (Biological Shield): This is the shielded room in which the irradiation process is realized. When the Irradiation Facility is operating, the Co-60 source rack is taken out of the water pool and placed among the boxes full of products. In order to avoid any radiation leakage out of the irradiation cell the walls and ceiling and floor of the irradiation cell are made of 180 cm thick concrete. 180 cm thick concrete barriers eliminate the gamma radiation formed by 3.0 MCi Co-60 sources and decrease the dose to an acceptable level for the employees and the environment. These protective concrete barriers are called biological shield. The thickness of the biological shield depends on the activity of the employed cobalt source and it was designed to meet the requirements of the International Radiation Protection Regulations. The personnel and product entry doors of the irradiation cell can be accessed after a maze for protection purposes.
5. Source Storage Pool: In order to turn the irradiation process off in the Irradiator, Co-60 source panel is dived into a 6-meter deep pool full of water. Co-60 source continues emitting gamma radiation within the water. On the other hand the water mass within 3.2 meters thick from the upper part of the source rack avoids the gamma lights to reach in the irradiation cell. In this way the personnel can enter to the irradiation cell without being exposed to the gamma rays and carry out the maintenance and repair works safely.
6. Product Storage Area: The product storage area in the gamma irradiation facility consists of two parts: unprocessed products storage area and processed products storage area. The products received are taken to the unprocessed products storage area and after they are prepared for irradiation process loaded to the conveyor. After the irradiation process the treated products are taken to the processed products storage area for loading to the vehicles.