Frequently Asked Questions
It is the amount of the energy that is adsorbed by the ionizing radiation in the unit mass of the substrate. 1 Gy is the 1 Joule energy that is adsorbed by a substrate weighing one kilograms.
Gamma irradiation has been applied with the aim of sterilization for a period longer than 50 years and there are more than 200 gamma irradiation plants in 55 countries world wide
In order to ensure the process control, the Harwell Perspex dosimeters, which are used for measuring the adsorbed dosage by the product, are used. In the dosimeter laboratory in Gamma Pak, the absorbance values at unit thickness are measured by spectrophotometer. The minimum and maximum dosage ranges of the product are determined through the evaluation of the dosage results obtained by statistical calculation methods and their compliances are confirmed. The calibrations of the dosimeters and other measurement devices in the facility are followed up regularly and their traceability by the competent authorities are ensured.
The irradiation of the products that were determined by the legal regulations as unsuitable for the irradiation, additionally the products that are about decomposed or decomposed, the expired products or the products that were previously subject to the other sterilization processes, the products with the damaged packaging or unsanitary packaging are not suitable for irradiation.
Gamma Pak provides uninterrupted 24 hours round the clock irradiation services including the weekends. The appropriate planning is performed upon the negotiations with the relevant people on the days and hours of the irradiation process either before of after the arrival of the products to the facility and the customer is informed accordingly.
The product boxes, which will be exposed to the gamma irradiation after bringing them into the irradiation room via automatic conveyor, are put inside the aluminum irradiation boxes (TOT) in their own packages without opening them. After the irradiation process, the irradiation boxes full of the products are taken outside the radiation room again automatically by the conveyor system and then the products are stored in the processed products storage area.
The inner dimensions of the aluminum irradiation boxes (TOT) are 56 x 62 x 122 cm and their maximum loading capacity is 125 kg. The most appropriate package dimensions that may be placed in the aluminum irradiation boxes (TOT) are indicated in the below table. If your existing packages cannot fit in those dimensions, your products will be placed in the aluminum irradiation boxes (TOT) with the possible most appropriate form.
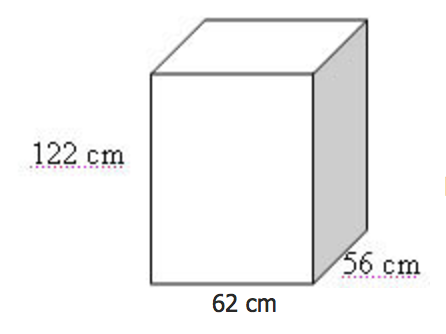
Dimensions of the Packages | Quantity of the Packages |
---|---|
55 cm x 30 cm x 40 cm | 6 |
55 cm x 60 cm x 30 cm | 4 |
55 cm x 60 cm x 40 cm | 3 |
55 cm x 61 cm x 61 cm | 2 |
One of the characteristics that make the irradiation process advantageous is the possibility of the products processed in their final packaged forms. The second one is the products safely presentation to the consumers immediately after the irradiation without the any requirements for any waiting period. When those characteristics are considered, the products arrived to the facility are irradiated in the irradiation process within the possible shortest time depending on the quantity (amount) of the products and their dosages. After mutual agreement on the delivery dates of the products based on the negotiation with the customer, the irradiation process is realized at the requested dosage and the products are delivered to the customer.
No. Because, in Gamma Pak A.S. the gamma energy of two gamma rays with energy levels of 1.17 MeV and 1.33 MeV are used emitted by the Co-60 isotope as the irradiation source. These energy levels of the gamma rays emitted by Co-60 isotopes are not sufficient to make any material radioactive. For example, the foodstuff exposed to the sunrays will not become radioactive and the human body will not become radioactive when we have dental X-ray or when we pass through X-ray devices at the airports for security checking purposes. Similarly, no irradiated products product by irradiation process will be radioactive.
The irradiation facilities are quite safe for the employed personnel and environmental concerns, because in respect to the radiation the facility is equipped with the interlock systems preventing entries during the irradiation process. In addition, the cell irradiation was designed with the 180 cm thick concrete walls, ceiling and floor in order to avoid any radiation leakage out of the irradiation cell, additionally the tightness of the source panel is guaranteed by the manufacturer company Nordion for a period of 20 years. When the source pencils finished, they are returned to the manufacturer company, so no radioactive waste will be created. In the operation of the irradiation facilities, the working personnel are competent and trained people. The personal dosimeters are used for measuring the dosages on the personnel and the dosages received by the employees are checked at regular intervals and their records are kept.
It documents that the irradiation was performed at the indicated dosage value of the gamma irradiations pursuant to the regulations and standards.
The irradiation certificate of the products are sent to the customer via the contractual courier within 5 (five) days after the products irradiated and shipped.
Prior to the irradiation process, a label showing that the products were processed in Gamma Pak and an indicator changing color radiation sensitively are affixed on the packages of the products. For the medical products, the yellow colored indicator before the irradiation turns into red color after the irradiation and for the foodstuff, the green colored indicator before the irradiation turns into violet color after the irradiation. In addition to those, the FDA [Food & Drug Administration] approved international green colored foodstuff irradiation symbol ‘radura’ [An artificial word combining the initial letters of the word "radiation" with the stem of "durus", the Latin word for hard, lasting] mark is affixed on the packages of the foodstuff for the indication of the performed irradiation process.
The following international corporations and organizations that are in consensus on the safety of the foodstuff irradiations in terms of health:
They have decided that consuming the foodstuff that were investigated by the aforementioned international corporations and organizations and that were irradiated at a certain dosage would not be harmful in terms of health and those would not create toxicological hazards.
As for the legal regulation, regarding the foodstuff irradiations in Turkey, there is the “Foodstuff Irradiation Regulation” that was initially published on the Official Gazette dated 6 November 1999 and was entered into force on the same date.
Together with some amendments throughout the world, usages of Ethylene Oxide and Methyl Bromide gases have been limited.
Some examples are as follows:
They have decided that consuming the foodstuff that were investigated by the aforementioned international corporations and organizations and that were irradiated at a certain dosage would not be harmful in terms of health and those would not create toxicological hazards.
As for the legal regulation, regarding the foodstuff irradiations in Turkey, there is the “Foodstuff Irradiation Regulation” that was initially published on the Official Gazette dated 6 November 1999 and was entered into force on the same date.
The worldwide consumer surveys revealed the following: It was observed that the consumers enthusiastic in purchasing the irradiated foodstuff, when they were informed correctly and basing on the scientific data telling that the irradiated foodstuff is safe in terms of health, that the foodstuff never become radioactive, that this type facilities create no hazardous environmental wastes and no hazards to the employees working in the irradiation facilities.